Seasons Greetings Cold Chain Colleagues,
As 2024 comes to a close, I want to take a moment to reflect on an extraordinary year and express my heartfelt gratitude to all of you—our customers, colleagues, and Cold Crew. Your trust, dedication, and partnership inspire us every day at US Cold.
Together, we are shaping the future of the cold chain, and I couldn’t be prouder of what we’ve accomplished.
I’d first like to acknowledge our customers. Your trust in us and commitment to shared goals inspire our team to innovate, excel, and deliver on our promises every single day. Partnering with some of the world’s most forward- thinking companies is an honor we don’t take lightly.
As we reflect on the progress we’ve made this year, I want to extend my deepest gratitude for your support and collaboration. Your success drives ours, and for that, we are truly thankful.
This year we accomplished several remarkable milestones.
We celebrated the openings of our Lake City, FL, and Tulare, CA, expansions and broke ground on new projects in Lebanon, IN, McClellan, CA, and Bethlehem, PA, and we’ve just announced the expansion of our Denton, TX, facility. These expansions are more than just growth—they are symbols of our commitment to innovation, reliability, and service excellence.
Across the country, our Cold Crew has risen to every challenge. Whether implementing cutting-edge technologies, collaborating across IT, operations, engineering, and the PMO, or ensuring our facilities operate at their peak, your dedication has set a new standard of excellence.
In logistics, our team faced a tough market with resilience and creativity, maintaining the exceptional service levels our customers rely on. Your unwavering focus and advancement continue to move the industry forward.
This year, we also celebrate the legacy of George Cruz, who has dedicated 43 years to US Cold. George’s leadership, mentorship, and customer-first approach have been pivotal in driving growth and shaping our culture. As he transitions into retirement in 2025, we thank him for his extraordinary contributions and the lasting impact he’s made on our company and the industry.
Looking ahead, 2025 promises even greater opportunities. With five major expansions and the upcoming launch of our new Customer Portal, we’re excited to enhance service, deepen relationships, and deliver more value.
The portal’s advanced features include the integration of AI, real-time inventory updates, shipment tracking, advanced reporting, and proactive exception management. All these features will streamline operations and provide actionable insights for our customers.
None of this would be possible without the incredible talent of our Cold Crew and the guidance of our Board. This year, we’ve seen multiple facilities and teams earn industry awards—a testament to your dedication, collaboration, and excellence.
As we step into 2025, I’m filled with optimism and confidence. With the best people, bold innovation, and a shared commitment to the future, we are ready to tackle new challenges and achieve even greater success.
Thank you for being part of this journey. Together, we are driving the cold chain forward. Here’s to a strong finish to 2024 and an extraordinary year ahead!
Happy Holidays, I wish you and your families all the best.
Larry Alderfer | President & CEO

Great Relationship, Growing Partnership
USCS and Gorton’s Seafood to expand Lebanon, IN, warehouse; welcome Gorton’s processing.
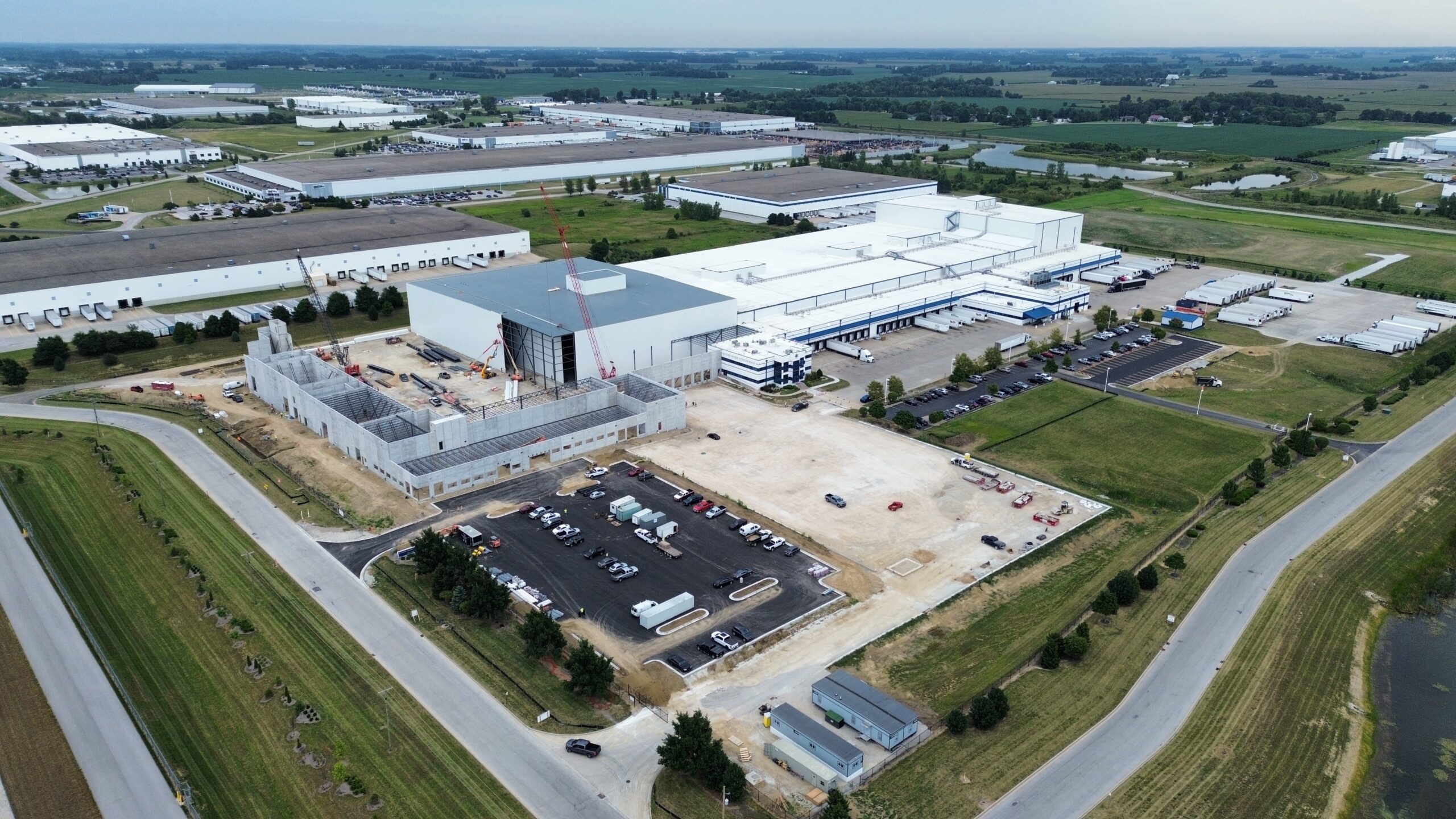
United States Cold Storage Inc. expects by next June to complete a 5.1 million-cubic-foot addition at its Lebanon, IN, public refrigerated warehouse, northwest of Indianapolis. In conjunction, Gorton’s Seafood, will construct its own attached seafood processing facility, which is scheduled to open in late 2025 and employ as many as 160 people.
“We set a goal to be a strategic provider and build long-term production support capabilities with specific customers to our portfolio,” says David Butterfield, US Cold Executive Vice President. “Today is just one wonderful step in fulfilling that goal. Gorton’s and US Cold have a 40-year relationship of working together as a distribution partnership and this greatly enhances that relationship in everything from raw material management to distribution of finished goods. It has been a great collaboration of efforts from both groups to truly create and design a state-of-the-art production facility with an automated warehouse to support all Gorton’s functions.”
“This year marks 175 years of Gorton’s spreading the goodness of the sea to households across America, so it’s fitting that in 2024 we can share this incredibly exciting news,” adds Kurt Hogan, Gorton’s Seafood CEO. “Our investment in this new facility, in partnership with US Cold, will allow us to continue our mission of making quality seafood accessible to everyone.”
Hogan said Gorton’s flagship facility in Gloucester, MA, will continue to serve as the company’s primary production hub while the new Lebanon facility will drive further growth with incremental production capabilities and distribution efficiencies.

Adam Ashley, US Cold Area Director- Midwest, says the two companies considered the warehouse and attached- plant proposition for nearly two years.
“After a facility tour—and considering Lebanon’s location, land availability and our nationwide COLDshare Consolidation (less- than-truckload shipping) program— we knew that US Cold Lebanon is the right place. Gorton’s has been a key partner for more than 40 years and this demonstrates the strength of that partnership.”
Acknowledged for Excellence
US Cold wins Ruiz Foods “Founders Award.”
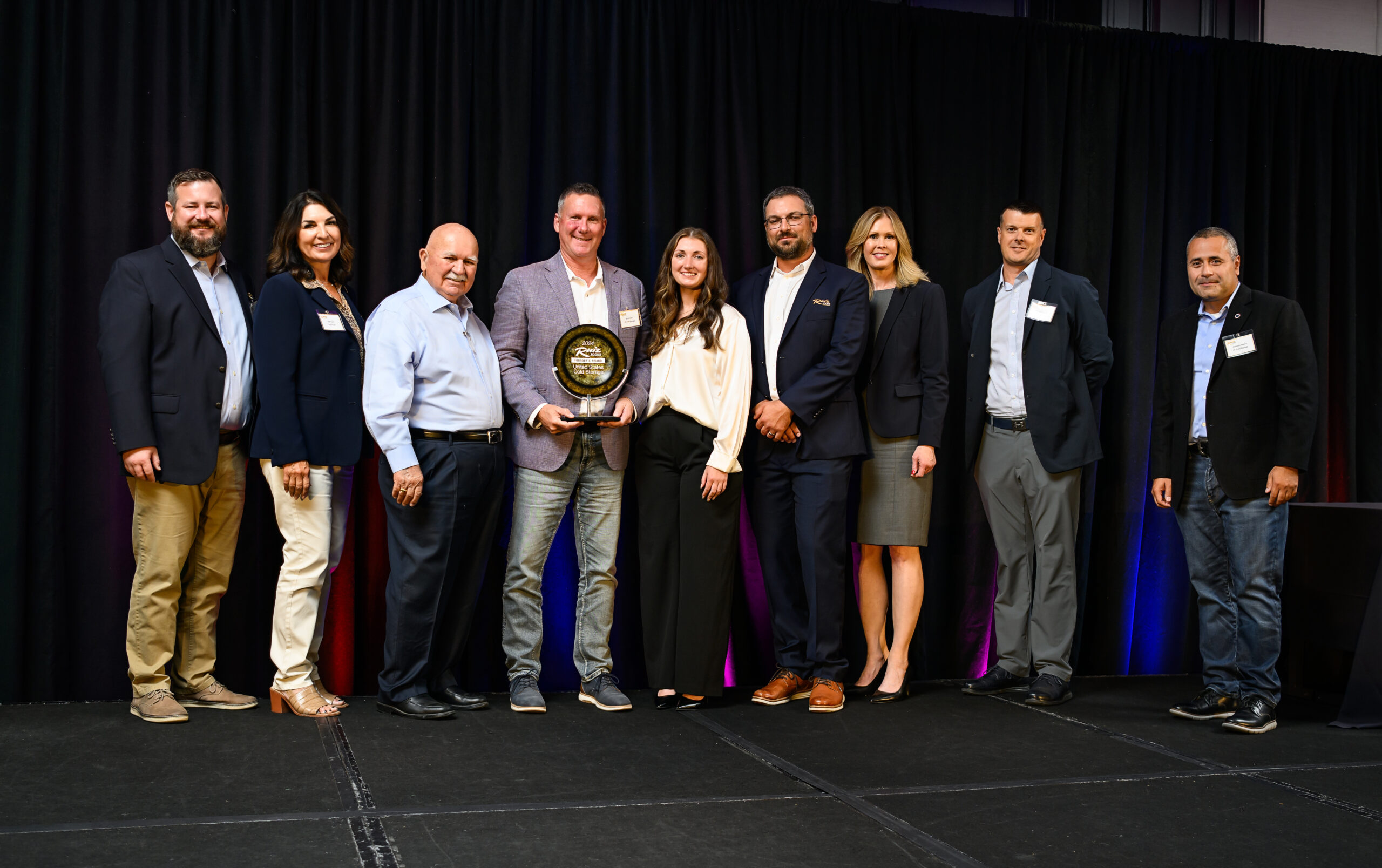
For the second consecutive year, United States Cold Storage was one of seven suppliers nominated and awarded during Ruiz Foods’ annual Supplier Summit. Family-owned Ruiz Foods of Frisco, TX, is one of the nation’s largest manufacturers of frozen Hispanic food products for distribution through retail, foodservice and convenience store channels.
With more than 40 suppliers/vendors in attendance, US Cold received the Ruiz Foods “Founders Award.” In part, it recognizes the two companies’ relationship, which spans more than 30 years. Ruiz Foods also discussed US Cold’s role in providing COLDshare LTL consolidation services to a major retailer’s Texas stores.
This award highlights not only the strength of our longstanding partnership but also US Cold’s continued commitment to delivering reliable, innovative logistics solutions. We are honored to support Ruiz Foods in their mission to bring high-quality frozen Hispanic food products to consumers across the country and look forward to many more years of collaboration and shared success.

Eyes on the Prize
USCS Wilmington embraces operations efficiency with “Department of Excellence” employee recognition.
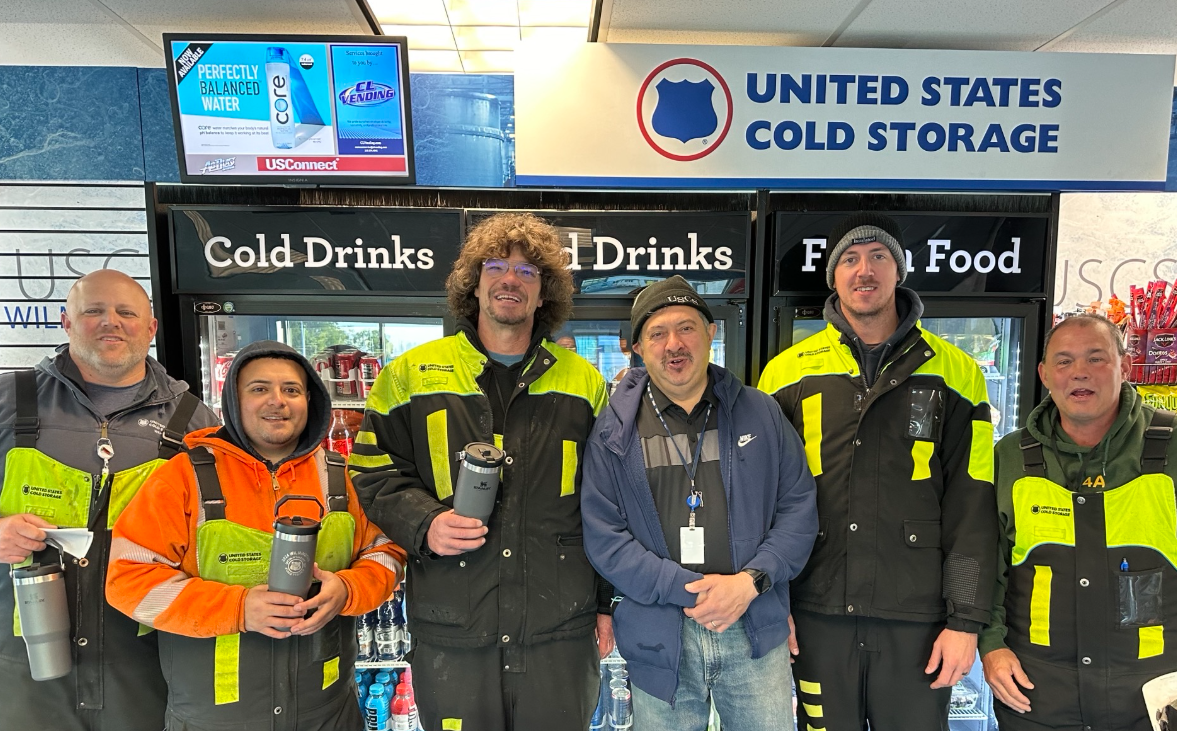
Not everything in business has to be overly formal. In fact, work can be so much more than work—when there’s an element of creative, incentivized fun.
That’s exactly the story at US Cold Wilmington, IL. When the Central Region first rolled out a Labor Management System in 2017,
Wilmington officials created a “Department of Excellence” (DOX) employee recognition program to literally make the transition a more rewarding experience. In 2018, Wilmington even enhanced and further customized its program allow warehouse associates to earn rewards through a four-tier structure.
“Our DOX program lets US Cold Wilmington acknowledge and celebrate outstanding weekly performances,” says General Manager David Salazar. “We offer associates the chance to earn exclusive rewards and recognition.”
All warehouse associates are eligible to participate and self-nominate based on performance achievements. To qualify, they must meet a weekly performance target of 105%, maintain at least 80% direct time, and uphold a discipline-free record. Successful participants are rewarded each week with a distinctive sticker, personally presented by their direct supervisor. Additional awards include US Cold-branded cups, clothing and other gear.
“The Department of Excellence program has not only recognized and rewarded outstanding performance but also has inspired a culture of motivation and achievement,” Salazar concludes. “By celebrating excellence, we’ve seen a significant boost in employee engagement. We’ve fostered an environment where our team is driven by pride, purpose, and the pursuit of continuous improvement.”
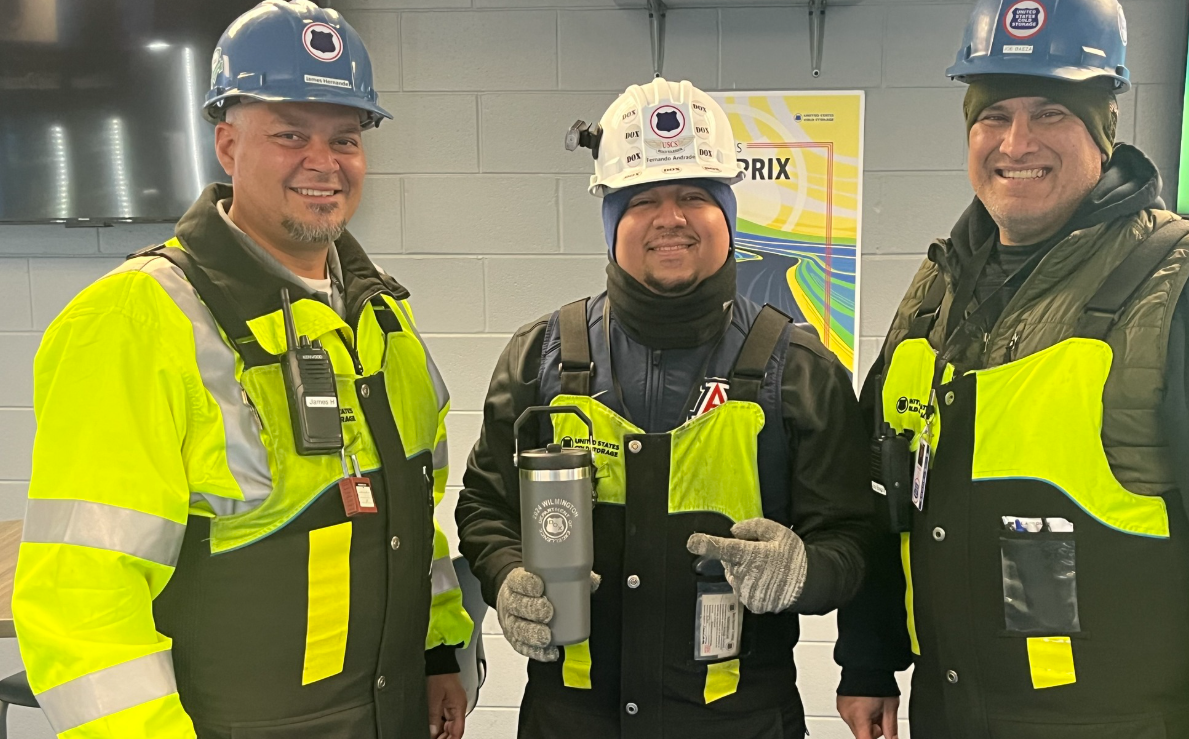
George Cruz—Legacy of Leadership
US Cold celebrates George Cruz, Senior Vice President, Southern Region
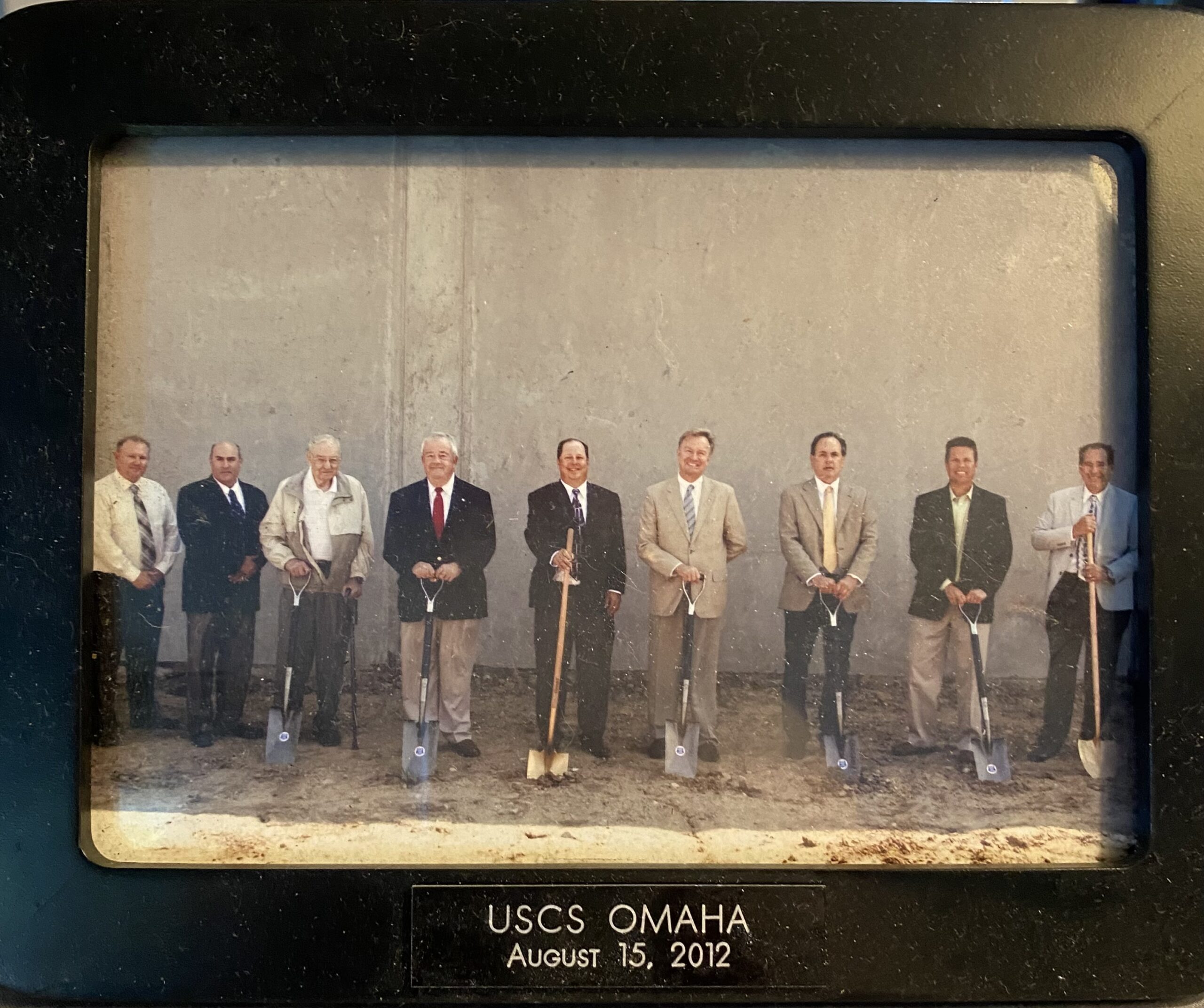
They say, “You get out of a job—what you put into it.” Then perhaps you also could say that what you get out of a career—reflects how much you invest in others.
Both sayings apply to George Cruz who will retire in 2025 after 43 years with United States Cold Storage. He started in 1982 as an Accountant at US Cold Miami. More than four decades later, his leadership legacy includes stories of building, expanding and shepherding company operations in Florida, Texas and Tennessee.
What began as roles in accounting and office management ultimately led to oversight for 13 warehouses stretching from Laredo, TX, to Lake City, FL. George’s impact and influence on US Cold is both highly recognized and will be highly missed.
Those who know George speak effusively about his competitive spirit—matched only by a compassion for others.
A Miami native, George joined the company in Miami as an Accountant in 1982. After two years, US Cold promoted him to Office Manager. Two years later he was on the move when US Cold transferred him to Dallas as North Texas Office Manager for operations in Dallas and Arlington.
In February 1990, he was appointed Operations Manager for US Cold Dallas and three months later, he was named Area Manager for all North Texas operations.
A passionate leader and learner, George utilized US Cold’s Education Assistance Program and earned his MBA (1998) in Logistics, Materials, and Supply Chain Management from the University of Dallas. Two years later (in 2000), he was named Vice President, DFW Metroplex; and in 2006 he assumed additional responsibilities for the company’s growing Tennessee and Florida locations. In 2015, he added US Cold’s Laredo, TX, area operations and one year later, was promoted to Senior Vice President.

“Debbie and his family, US Cold, good wine, cigars and the love of travel are all things that jump to mind for me when I think about George. George is and has always been a man in motion, a man with a plan and a leader who tirelessly focuses on what is best for US Cold, our customers and our Cold Crew. For as long as I’ve known George, he has wanted to be accessible to all of his customers. George has the gift to be able to develop relationships with anyone and find common ground, listen and learn what is important to people. This allowed him to both understand customer needs and create solutions and simultaneously understand the US Cold Crew and support his team no matter how difficult or challenging the circumstance.
Finding the balance between these two key groups in our business has been George’s superpower. George’s career has been amazing. He has taken on every challenge, driven massive growth in our Texas business over the years, and jumped in to support anyone or any facility that needed help. He has done it all and succeeded in all and always took care of his business. George will be missed!”
Larry Alderfer
President & CEO, US Cold

“George and I became very good friends over the years. He’s a special person and has had that effect on so many people. He’s family oriented and has always treated the company like a family. For that reason, people are always pleased to work with him. Professionally, George also is something of a perfectionist.
He wants to do things right and well and is extremely competitive. And not only would that involve our competition but he also wanted his region to be the best within our company. It’s all good and that’s simply how George is wired.
He has accomplished everything we’ve asked—everywhere he’s gone. George was hired in Miami as a bookkeeper and within six months, he turned around the accounting program. Whereas Miami had always been last to submit its monthly reports, he submitted his report first and the quality was so much better.
He went to Dallas as office manager and it wasn’t long before he took over our entire Metroplex operation. He wanted to grow faster, offer better programs and establish US Cold as the Dallas area cold storage leader. Not only did he turn that operation around—he also grew the business quickly through an expansion in Arlington and a new warehouse in Ft. Worth.
When George took over Florida, he improved those operations. Soon things were better in Miami and Orlando and we grew into Lake City, which continues to expand. And when we were in tough shape in Tennessee, that became part of his region and he literally almost moved there while running the region. Not only did he turn our facilities around but even labor issues went away as employees bought into his passion and philosophy.
Everywhere he’s gone, George fills the space and has done what he’s needed to do. And while he has had an amazing career with great financial performance—his effect on people has always been special. He truly makes people want to ‘buy in’ and become something more.”
Dave Harlan
Former President & CEO, US Cold

“When I think about US Cold, George Cruz is the first person I think of. I started with the company under George more than 30 years ago in a position that I later learned he had helped shape. From that moment forward, he encouraged me to push myself professionally. My pursuit of “understanding the big picture” and “understanding the whys” behind just about everything, came from him.
There are two things about George that I know to be true: his commitment to US Cold and his sincere commitment to those working for him.
He set the example by always pushing himself for his best and encouraging those around him to strive for the same. He always challenged his leaders to question the status quo and to never shy away from difficult undertakings. When facing obstacles, he always did his work to understand the requirements and the objectives. Subsequent conversations always would include those involved sharing their perspectives, but he would typically save his views until the end.
He encouraged open communication—yet guided discussions in a positive way that brought about shared learning and collective decision making. In the end, you couldn’t help but come away with a broader perspective and more knowledge.
George’s quest for growth and success—both personally and professionally—is contagious and this will live on in those that he has mentored. George definitely blazed many a trail, yet his approach to vision and leadership formed the foundation upon which many successful operations now rely.
George has had such a positive influence on my life. He hired me at US Cold and got me started on a professional path that I had never considered. He helped equip me with invaluable skills and has painstakingly instilled in me the belief that through hard work and dedication, I can accomplish anything. His “never settle” and “always move forward” attitude is forever engrained in me. He always made it appear so easy and simple, but I have since proven otherwise.
Through the years, he has served as my boss, my mentor, my sounding board, my cheerleader, my coach and my friend. The latter is what I hold most dear. George is always there with a friendly supportive voice.”
Michelle Grimes
Senior Vice President, HR

I have worked for George for 25 years. There have been uncountable professional accomplishments that I could recall. But there is another side to George, the side I appreciate most. It involves all of the personal things George has done for me. He has a shown me that we are not all just numbers doing a job. Instead, we are people who deserve to be treated as such. George has been there for his people in times of need.
Although I can’t speak for them, I can for myself. Lots of things happen during the course of 25 years and George was there when I needed him. He was supportive through my father’s long-term illness. He repeatedly told me that family came first. I believe the last letter my dad ever wrote was to George—as he thanked George for allowing me to spend time with him in his time of need. When my mother had a heart attack, I flew to Ohio to be by her side. When I called George, he was sad for me. The last thing he said was “to do what is best—and I will see you when you return.” George’s compassion was not limited to just his employees.
George gave my wife a rosary more than 20 years ago. It has helped her many times over the years. In this business, we have often said that anyone can put up four walls and keep it cold. Yet it takes people to make it successful. George understood that. He was grateful for the people who supported him. His actions throughout the years are a testament to the person he is.”
Frank Monroe
General Manager, Ft. Worth
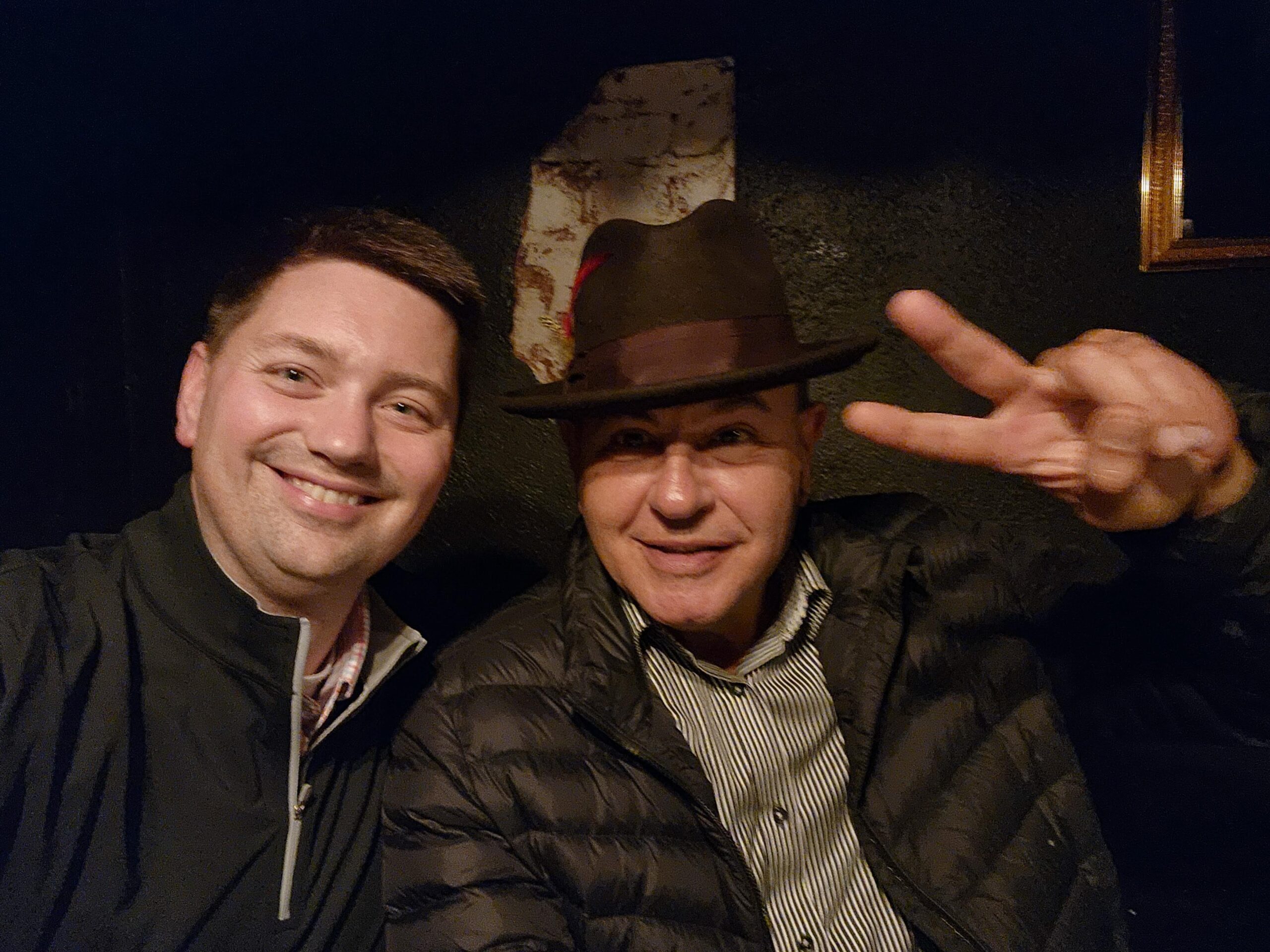
Partners in Progress
Annual Carrier Conference honors carrier partners, spotlights new programs.

You might not think about it at first but even people engaged in transportation, focused on a world of motion—need to occasionally pause, sit and enjoy the moment. And that’s just what happened in early October when US Cold hosted its annual Carrier Conference outside Chicago. It drew approximately 160 attendees including 130 representatives from as many as 75 different carriers.
“It’s very important that US Cold keeps its carrier partners close and informed,” notes Michael Carlisle, Senior Director, Logistics Operations. “Many of our carriers are small to midsize and this is a great way to network and educate them about the market as it pertains to US Cold freight. We also wanted to show our carrier-partners what US Cold does for its customers to stay competitive and provide the best customer service.”
Carlisle credits US Cold Midwest Logistics Manager Brittany Vadeboncoeur for planning the one-day conference with three primary components: education, a live podcast (“The Cold Cast”) and an awards dinner.
We appreciate all the hard work and dedication from all of our carriers. All of our carriers stand out with their exceptional service and growth with US Cold. In an environment where there are more carriers than freight, US Cold stays true to partnerships and commitments. We are fortunate to have carrier partners that do the same for US Cold. We look forward to continuing these long-standing relationships with these carriers and our entire carrier community. They are truly the reason we can continue to service our customers with ‘Best In Cold’ consolidation and transportation services.”
Mike Carlisle
US Cold
Conference Program
US Cold’s education program had five presentations about:
-
Carrier Engagement: Presenting were US Cold representatives Jennifer Lantro, Logistics Operations Supervisor; and Marc Vendome, General Manager, Logistics. They outlined US Cold’s new Carrier Engagement structure and introduced new engagement coordinators assigned to measure carrier performance. For some carriers, it was the first time they could meet their respective coordinators in a face-to-face setting. There also was update about US Cold’s carrier bid program.
-
Load Tracking: Julia Kruy, Senior Solutions Advisor, FourKites, Inc., discussed US Cold’s new load tracking initiatives. Notes Carlisle, “In a world where you can track your package all the way to your front door, we need to be able to show our customers real-time visibility of their freight.”
-
SmartMove: This was a highlight on US Cold’s newest technology, SmartMove. SmartMove is automating load building and making better data-driven decisions for consolidated freight. Presenters were Luis Sanchez, Supervisor, Automation and Analytics; and Reiner Scherzinger, Continuous Improvement Specialist.
-
Carrier Market Update: RXO Inc.’s Corey Klujsza, Vice President, and Kevin Adamik, Director, Procurement Analytics, discussed overall carrier market conditions and how they impact US Cold’s business.
-
Carrier Check-In Program (Vector): This was a panel discussion about US Cold’s growing Vector program and its steamlined check-in process for arriving carriers at US Cold locations. US Cold has a live program at four of its sites. Panelists included US Cold Minooka, IL, representatives Matt Reed, General Manager; and David Dicharo, Superintendent. Others included Nina Stojanova, Operations Manager, TRX Express; Nicholas Schmitz, Manager II, Operations at J.B. Hunt Transport Services, Inc.; and Andrew Dieter, Owner, Joe Dieter & Sons Trucking.
Dr. Anna Johnson, Vice President, Corporate Development, Marketing & PMO, hosted a live panel discussion— recorded as a podcast (“ColdCast”) about current market conditions and future predictions. Panelists included US Cold representatives:
- Michael Carlisle and Brian Magnus, General Manager-Midwest Logistics
- Korey Ackerman, Owner, K&B Transportation
- Brent Higgins, Founder, Brent Higgins Trucking
- Anna Dittoe, Director, National Accounts Division, MegaCorp Logistics.
US Cold Carrier Awards
United States Cold Storage uses its annual Carrier Conference as its platform to present awards in seven categories. Carriers are evaluated by as many as five key performance indicators.* Carrier of the Year winners for 2024, by category, were:
National Award: Marten Transport
Carrier Partner: TRX Express
Midwest: Joe Dieter and Sons
Northeast: Iceland
Southeast: Werden Logistics
South: Five Star
West: Mendoza Trucking
Welcome to Lumberton, NC
USCS gives SHIELD readers an inside look at operations within its coast-to-coast network.
Located in the heart of North Carolina, US Cold Lumberton boasts one of US Cold’s largest blast-freezing operations. With 60% of inbound loads coming from local processing plants, it handles an immense volume of export shipments and sends products worldwide.
US Cold Lumberton also is BRCGS Certified, which means it meets rigorous international supply chain standards and is globally recognized for food safety and quality. Many Lumberton customers have been with the operation since it opened in 1988, and its team goes the extra mile to ensure customer needs are met. This personal touch extends to every level of our service—from working closely with customers on logistics to making sure their products arrive safely and on time.
“Our customers own the product, and our job is to make their experience with us as easy and efficient as possible,” says Office Supervisor Denise Bryan.
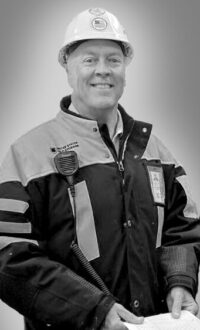
Over the years, I’ve watched this facility grow into a cornerstone of US Cold’s operations, and I take pride in the family atmosphere we’ve built together, At Lumberton, we believe in leading by example. I’ve done many of the jobs my team performs today, from operating forklifts to managing blast- freezing operations. Our open-door policy encourages open communication, allowing us to work together to meet challenges head-on and foster a positive work environment.”
Steve Musselwhite
General Manager, Lumberton NC
Safety also is at the heart of the Lumberton facility. The facility’s safety program has led to significant milestones, including a current streak of more than 379 days without a lost-time incident. Lumberton participates in US Cold’s company-wide safety competition and has been tied for first place in its track—a testament to its dedication to the team’s well-being.
US Cold Lumberton also is dedicated to sustainability at its core. Lumberton houses the largest solar array in the US Cold network and this produces up to 19% of the site’s daily energy needs. US Cold plans to expand this this capacity to more than 30% in the coming years.
In addition to solar energy, the site has reduced CO2 emissions by 655 metric tons simply by changing how we order supplies. US Cold Lumberton is proud to be an industry leader in sustainability and continues to seek new ways to reduce its environmental footprint.
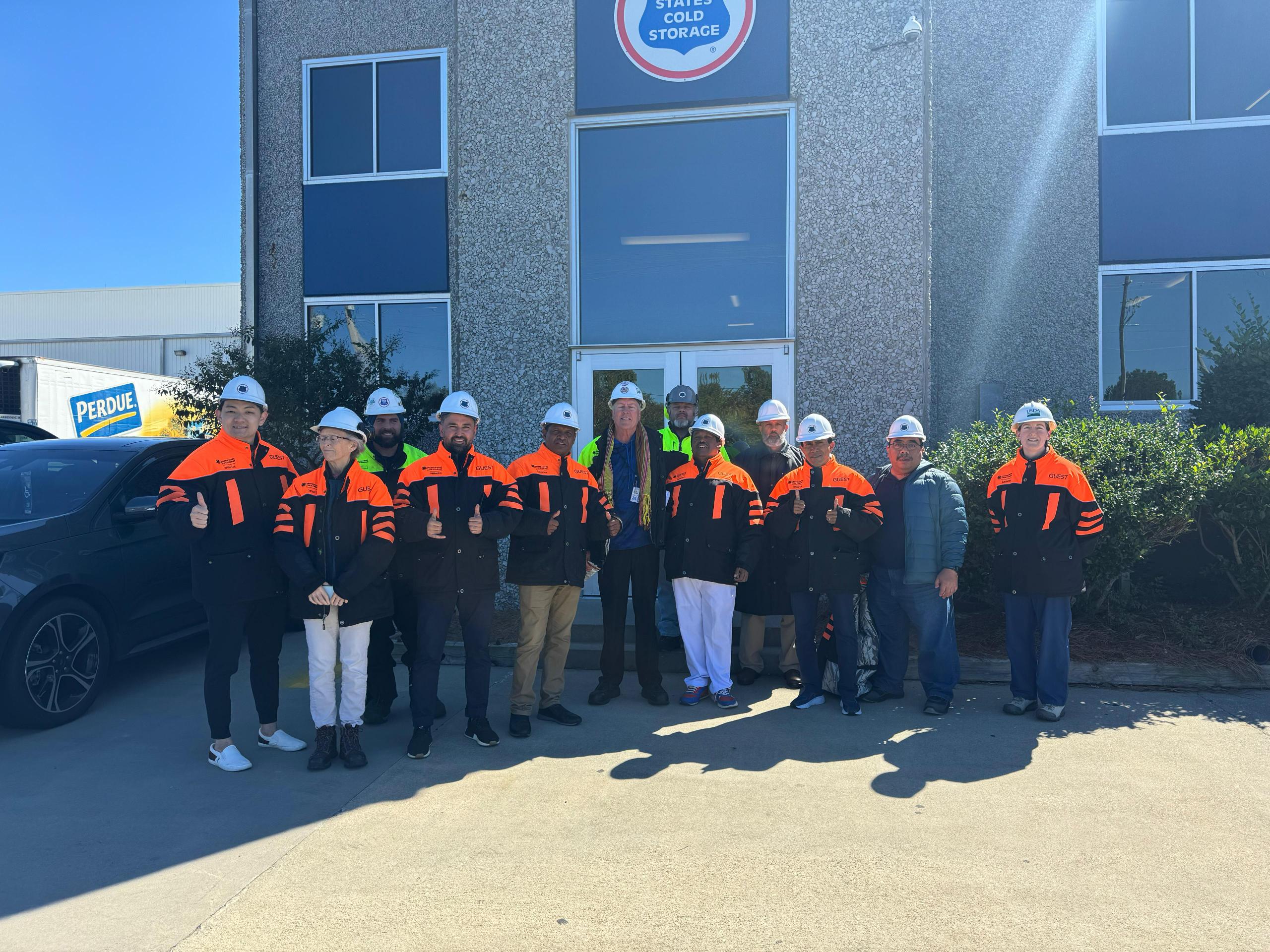
Cold Company—Warm Heart
“Connect for a Cause” engages US Cold employees with communities, non-profit programs.
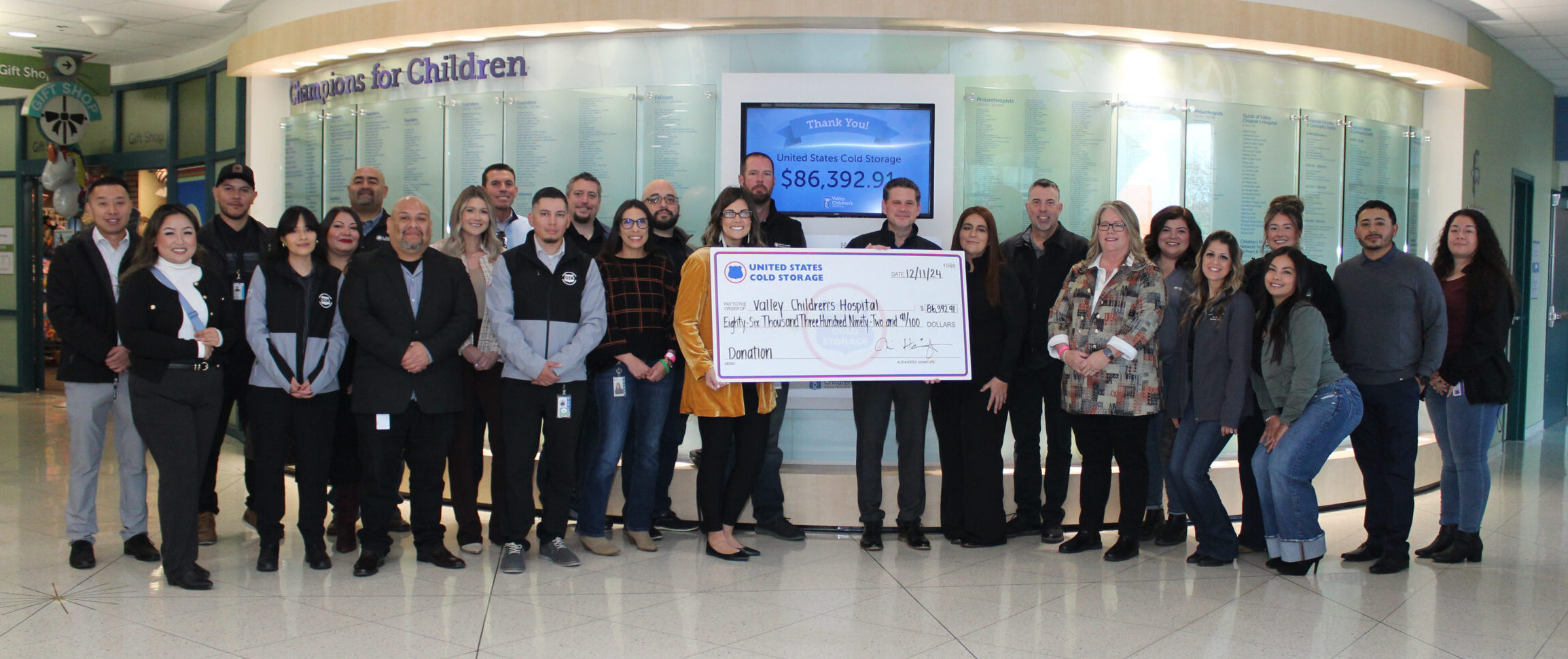
Pardon the play on words but there’s definitely a warm side to United States Cold Storage. In October, employees completed their fourth annual Connect for a Cause (CFAC) campaign that raised funds, volunteerism and community outreach for non-profit charities.
This year’s event raised $269,907 across five employee regions. Those participating included employees at US Cold’s Camden, NJ, headquarters as well warehouses in four regions. This year, US Cold’s “Cold Crew” selected and partnered with
The Alzheimer’s Association
Pediatric Brain Tumor Foundation
Valley Children’s Healthcare Foundation
Christ’s Haven For Children
Utah Parent Center
St. Jude Children’s Research Hospital
Tunnel to Towers Foundation
Children of Fallen Patriots
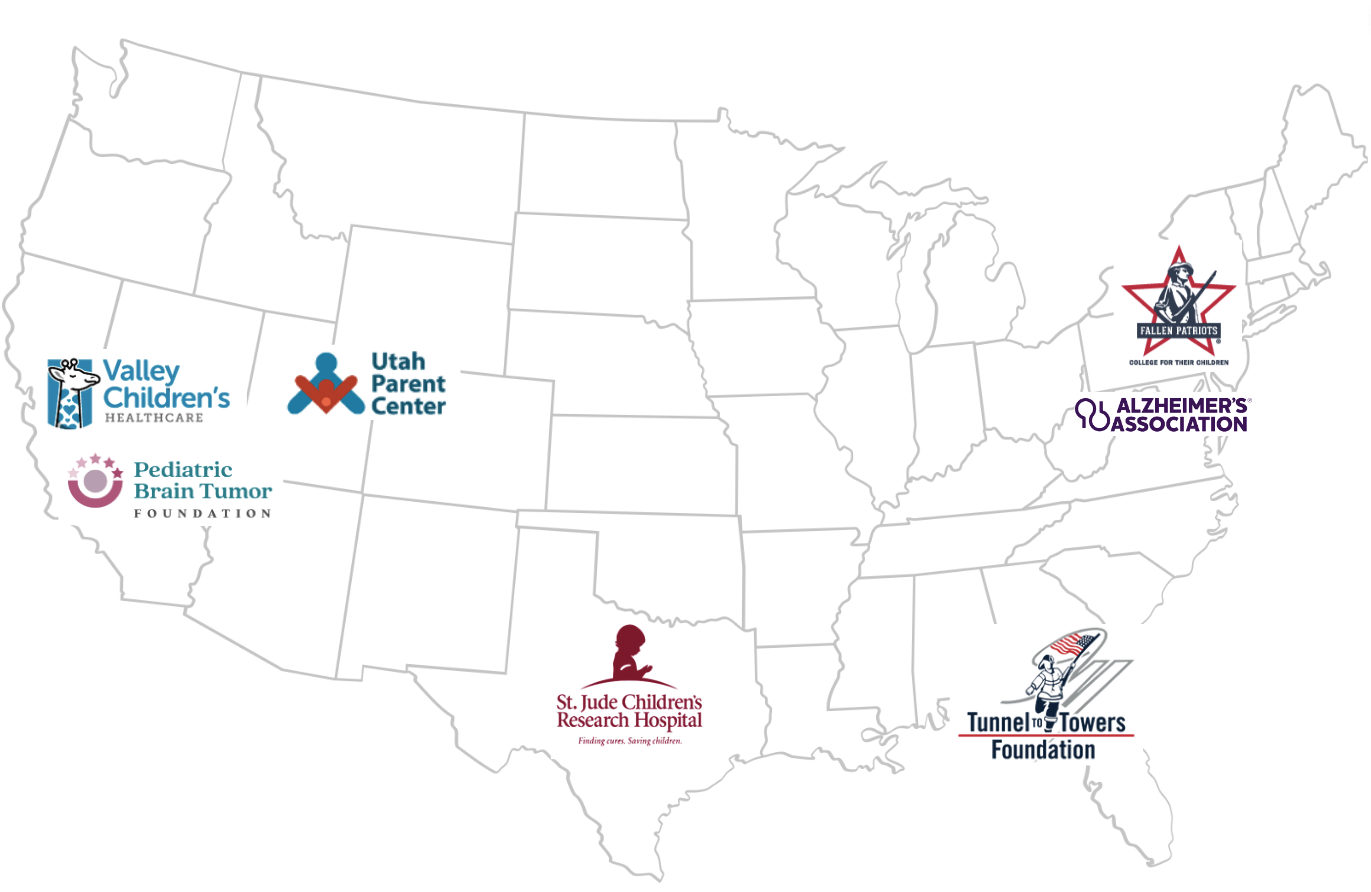
Connect for a Cause continues to be a way for employees to connect with their coworkers, community, and a meaningful cause. United States Cold Storage is a dedicated community partner and encourages its employees to donate time, talent, and treasure to help ensure that the programs, services, research, and outreach that nonprofits provide continue to flourish. It’s part of being a good corporate citizen.”
Paige Salvador
HR Manager, Employee Experience
US Cold thanks all its employees for their time, service and giving with this year’s Connect for a Cause program. Likewise, the company acknowledges the efforts of more than 45 CFAC Ambassadors and five area leaders. Area leaders included …
… US Cold Camden, NJ: Dominica Veneziano, Business Development Associate
… West Region: Chris Halsted, Regional HR Manager-West
… Southwest Region: Carol Fitzgerald, Staff Accountant, and Kathy Yarbrough, Area Customer Account Manager
… North Region: Max Sheffler, Training Quality Safety Supervisor
… Southeast Region: Nicholas Dimsdale, Industrial Engineer
“As we near the conclusion of this year’s campaign, we celebrate the hard work, generosity, and passion of every employee who has contributed,” said Salvador. “When we come together for a cause, we do more than give—we transform lives. This campaign is proof that our collective effort can spark real change for those who need it most.”
Less (Waste) is More (Appealing)
US Cold embraces waste reduction for more sustainability.
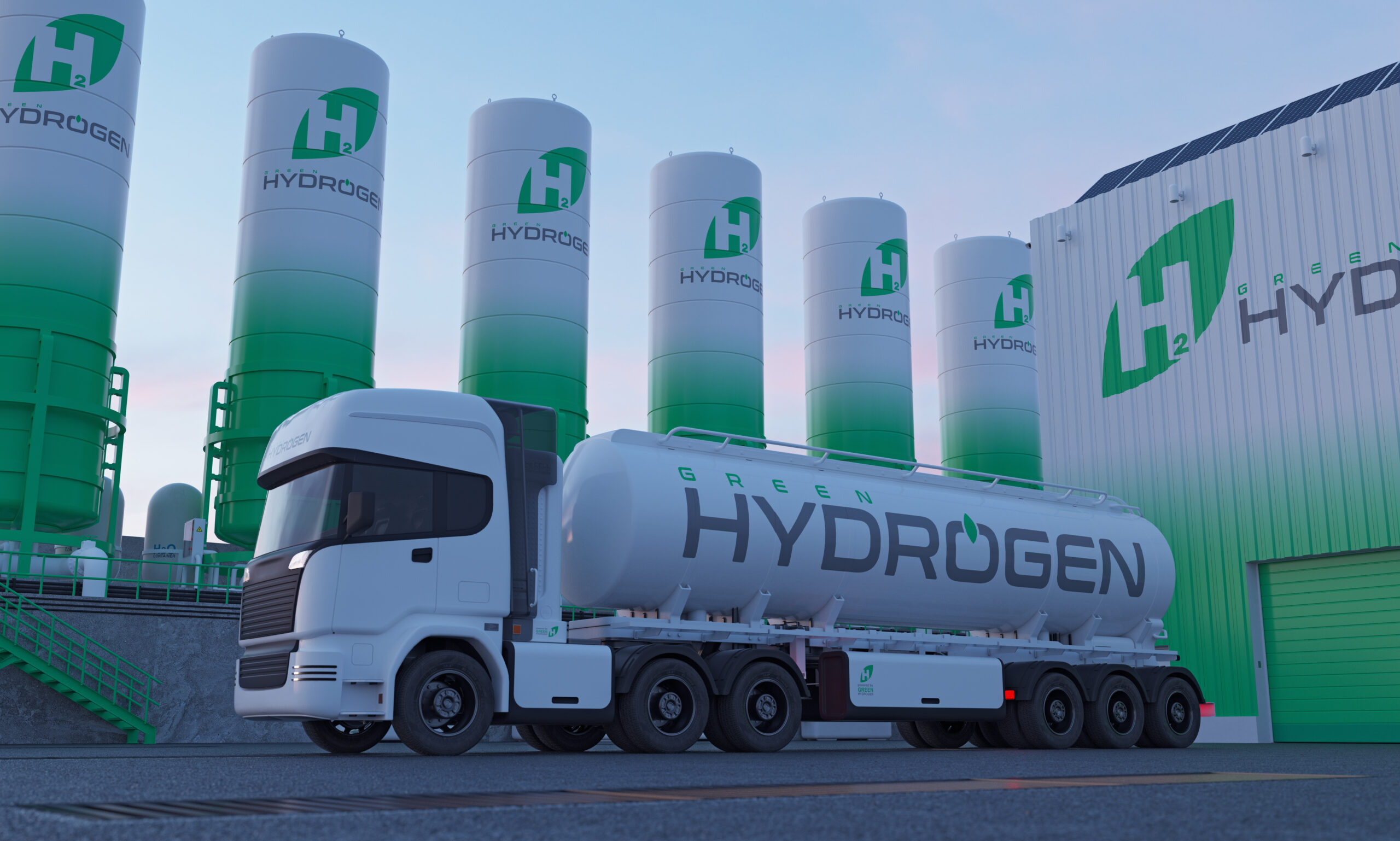
When you’re one of the nation’s largest cold storage and logistics providers, it’s natural that sustainability discussions focus first on energy efficiency and reduction. Then again, when you have a national network of 38 sites handling the nation’s food, even smaller sustainability measures—including those to reduce food waste—have a big impact.
In 2024, US Cold cast a vision for all products passing through its facilities to either be consumed or converted into compost, feedstock or renewable natural gas. US Cold facilities coast to coast embraced multi-disciplinary efforts to eliminate food waste and to date, the company has diverted an estimated 3.7 million pounds of product from landfills.
“Our program identifies beneficial uses for food wastes and recyclable materials that would otherwise be landfilled. The idea is to convert these materials into raw material for soil and land improvements as compost, animal feed supporting US food supply, or renewable natural gas supplied to the local grid. In less than a year, we have taken this project all the way from the brainstorming stage to widespread implementation,” adds Henry Lewis, US Cold Sustainability Specialist III.
“Our project team is tremendously excited by the early progress we’ve made our partner organizations and we’ve effectively established a landfill diversion option at each US Cold site across the country.”
This program focuses the recovery of organic material and promotes circular business models where resources are preserved and never lost. This is aligned with John Swire & Sons Ltd.’s SwireTHRIVE Waste Pillar.”
Sara Cook
Sustainable Development Manager
Cook and Lewis note that a few operations, including US Cold McClellan Park, CA, already were diverting food waste from landfills as a customer service and in conformance with state regulations. Likewise, Cook and Lewis credit US Cold Bethlehem, PA, for running the company’s pilot program efforts; and US Cold Arlington, TX, for embracing the program at such a large scale.
“Our Business Intelligence team has been outstanding by compiling and refining all the data related to this aspect of our business,” notes Lewis. “That enabled us to conduct detailed conversations to optimize solutions with our sites, our customers, and our waste partners. In the end, we believe this program will help customers reach their own goals related to zero-waste, circular economy and emissions reductions. We can help them—both by tangibly improving the processing of physical waste and also by improving our data accuracy.”
Automation: Where Cold Temp Meets Tech
USCS Engineering forms Automation Group to better guide fast growth and support existing automated operations.
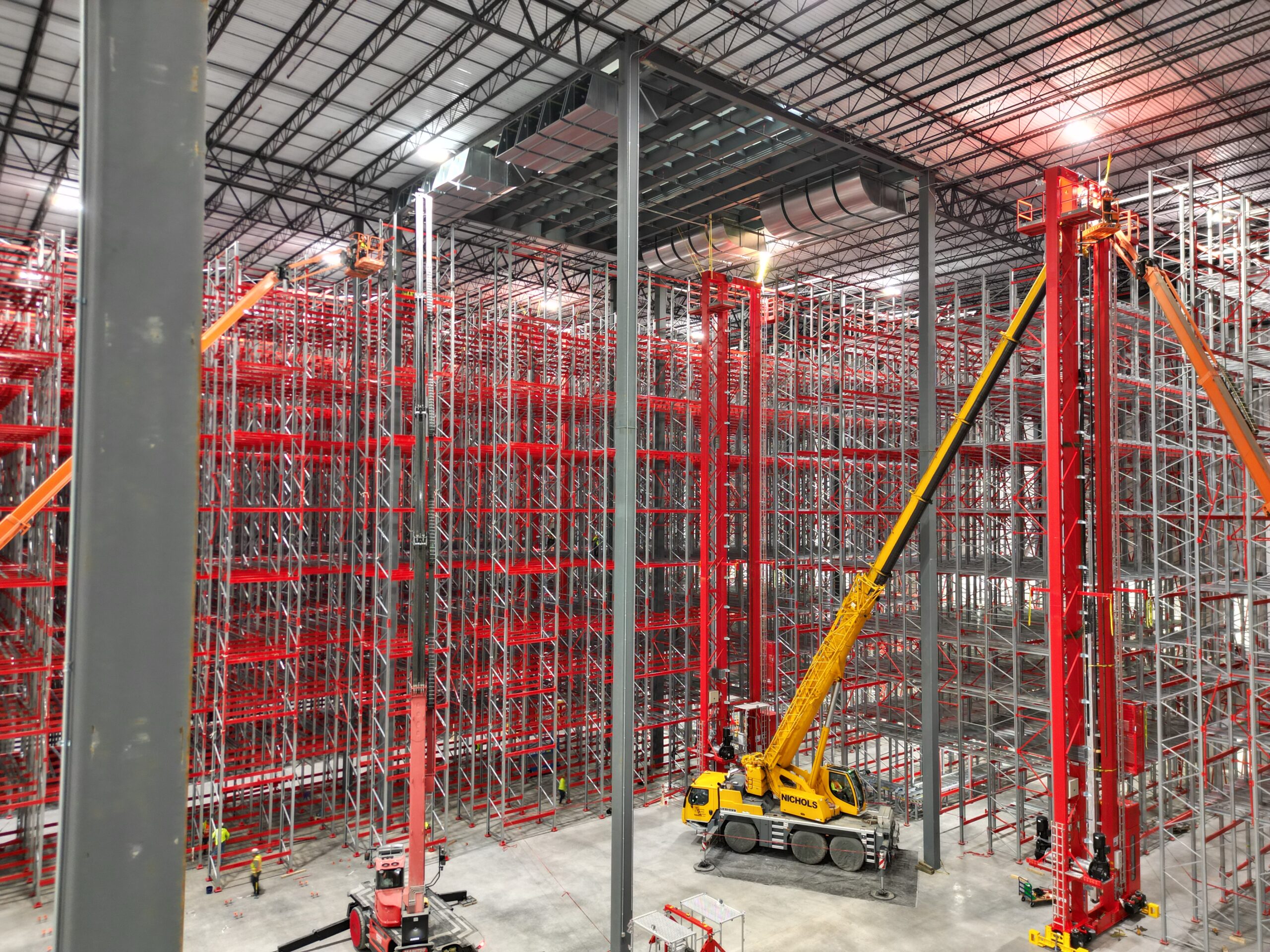
They say you can use numbers to support any story. Yet this is a case where the numbers tell an amazing story of their own. Officials project that by year-end December 2027, US Cold will have approximately 104.3 million cubic feet of automated cubic feet in operation and that will represent nearly 24% of US Cold’s total cubic feet. Moreover, from 2023 to 2027 that will reflect a 300% increase in automated storage space.
Strategically, US Cold also is committed to a position that all future growth include some level of multifarious design that incorporates either fully automated ASRS and/or semi- automated VNA storage space. This will further increase US Cold’s total automated systems in operation and operational space.
Considering these moves, US Cold’s Sustainable Engineering department created an Automation Group in November 2024 and promoted Mark Schuchter, former Senior Manager of Automation, to a new role as Director of Automation and Technology.
As the company continues to grow, and more automated systems and space is brought online, it is paramount that US Cold have the appropriate structure and resources in place to support all current automation systems, as well as, effectively design and construct future automated systems. The current automation group structure was not sustainable long-term and therefore needed to be restructured.”
Mike Lynch
Senior Vice President, Sustainable Engineering